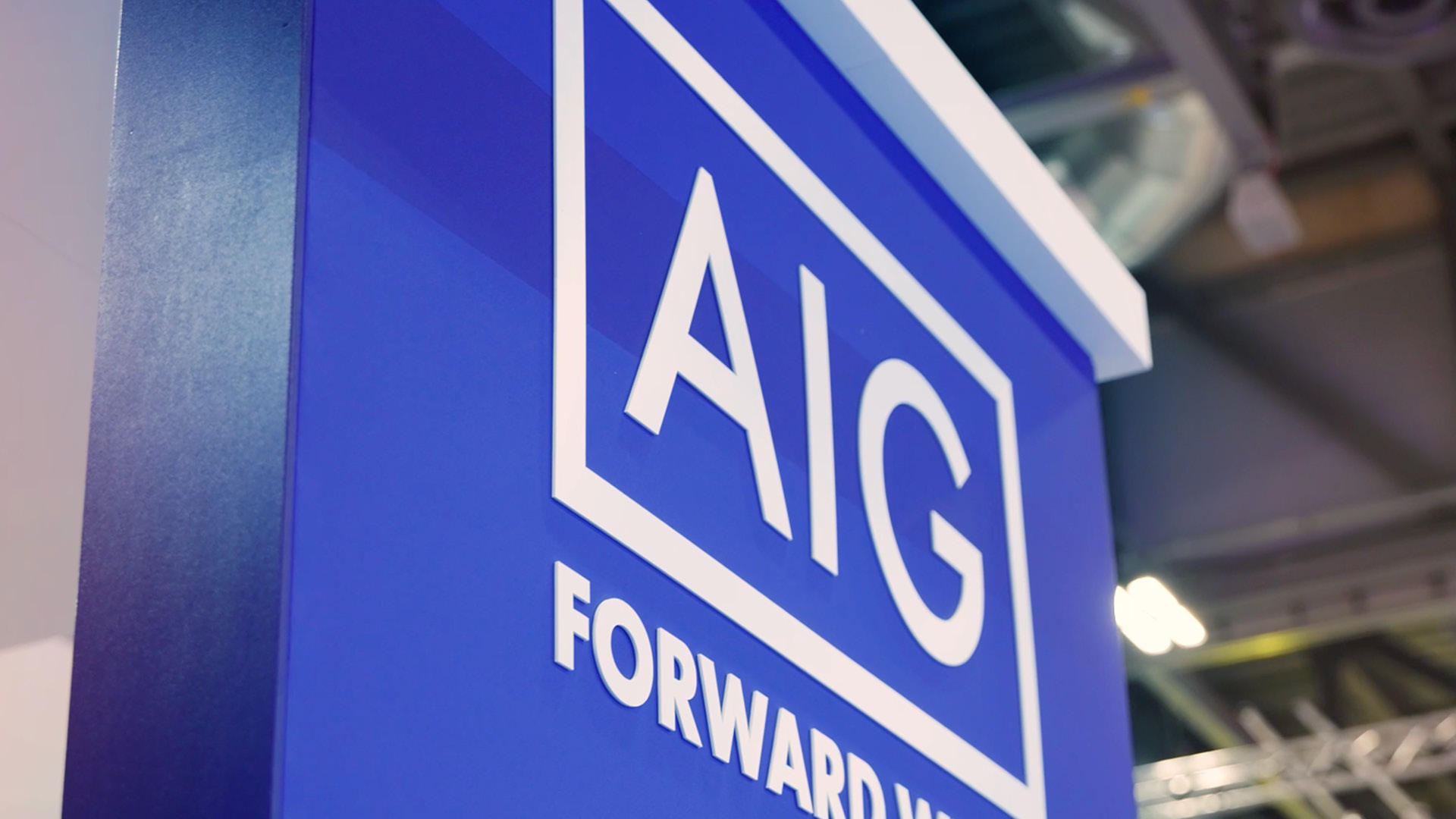
AIG recently attended the Association of Insurance and Risk Managers in Industry and Commerce (AIRMIC) conference in Liverpool. Over three days, AIG UK, Global Specialty and Talbot Underwriting colleagues engaged in meaningful conversations with clients and brokers, deepened partnerships and explored ways to prepare for complex risks.